AT the Ministry of Infrastructure Development (MID) yard in Honiara, the project staff produces a significant number of blocks daily. This endeavor is a part of the activities of the Interlocking Block Pavement (IBP) technical cooperation project, supported by the Japan International Cooperation Agency (JICA) and carried out by the Ministry of Infrastructure Development (MID).
The project aims to introduce IBP as a standard road pavement method in the Solomon Islands.
The mass fabrication of interlocking blocks only by hand and with small equipment started in early July 2023 and is scheduled to continue until October. There are two primary methods for producing interlocking blocks: one uses a heavy concrete block-making machine, and the other uses plastic molds and a vibrating table. The project introduces the latter method for local companies with small initial costs and suitability for small business start-ups.
Clearish Kosoi, a project staff member who has been working on the project since the beginning said: “You will find many plastic molds, a concrete mixer, and two vibrating tables at the MID Yard. The materials used—cement, aggregate, sand, and water—are commonly used for concrete production.
“This initial step involves applying oil inside the plastic molds, like greasing the cake pan, and we’re using used cooking oil for these blocks.
“Through this mass fabrication, participants can learn the techniques and knowledge of interlocking blocks, their production, and quality management to become trainers of IBP to teach others and promote this technology,” she said.
Clearish is calling for interested participants to join them.
“Some interested parties, such as SINU students and local construction companies, have been visiting and participating in the block production process,” she said.
Lisa Masodo, a MID Yard officer assigned to the project since April 2023, said that the project team has conducted multiple tests to determine the optimal proportions of mixing materials.
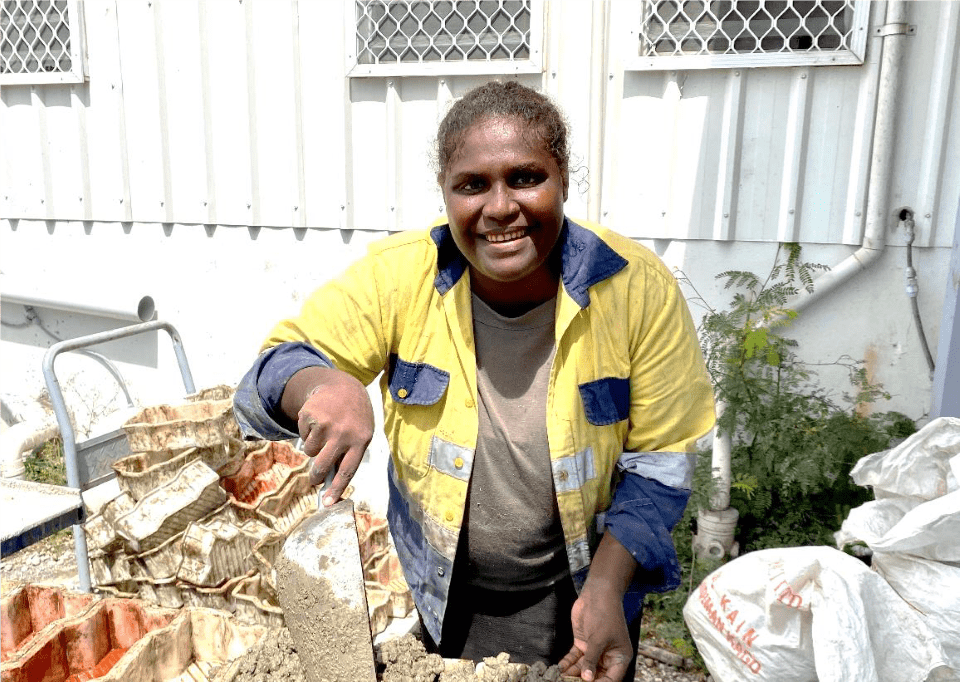
“Initially, we began with the proportions set for hand-bang mixing. Still, we were astonished by the effectiveness of the vibrating table. This led us to reduce water, producing stronger concrete blocks.
“The project team is encountering difficulties due to variations in ingredient moisture caused by rain and contrasting dry conditions. However, this will be addressed through careful monitoring and adjustments in the production processes to ensure consistent quality and optimal results,” she said.
Lisa said: “It’s been a great learning experience making blocks, and I wish MID would continue producing these blocks even after the project is finished. I want to be part of that block production, too”.
“The IBP technique can be utilized easily by anyone and applied anywhere, unlike the generally conceived road construction with heavy equipment and machines and male workers. The blocks produced will form an 80-meter-long, 5-meter-wide paved road in the middle yard. Approximately 13,000 blocks are required. The expected production period is around four months,” she said.
Meanwhile, Fiona Siosi, another MID officer working at the yard said her concern is the safety measures of the workers.
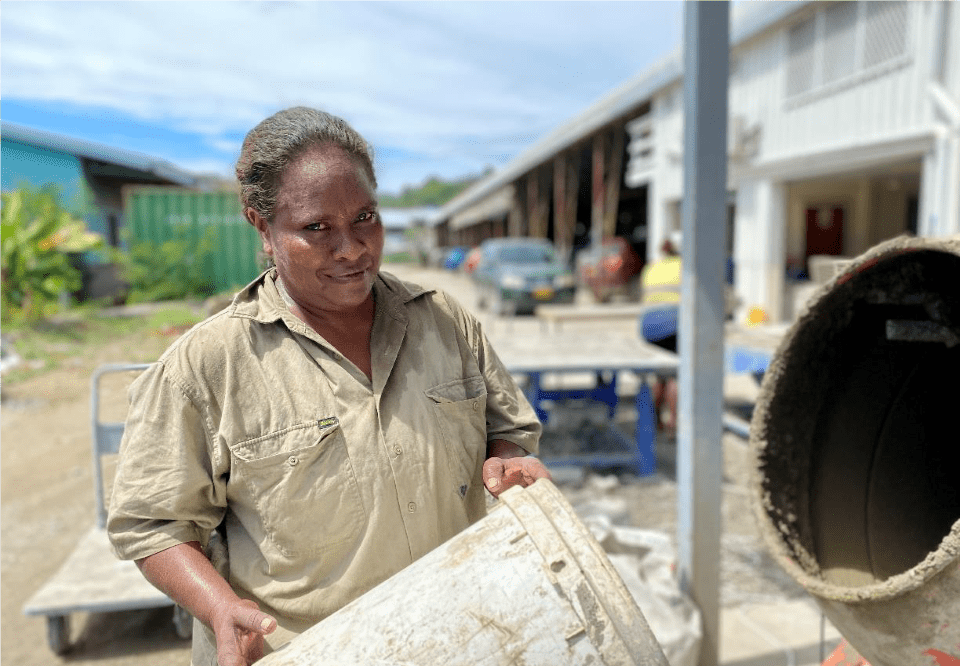
“We have been producing for five weeks and achieving a steady pace of making 200 blocks daily. On the first day, we could only produce 60 pieces. Now we have three times more expertise.
“I’ve been helping the project with the block production, and it has been an interesting experience learning new techniques”, Fiona said. “This can also be applied in Munda. My home village, where extensive development around the airport is ongoing.”
Interested Participants Wanted:
IBP has the following features:
1. Blocks can be manufactured using simple equipment and techniques, and construction can be done manually without heavy machinery.
2. In the case of cracks, fall-off, potholes, or other defects in the blocks, they can be easily patched by removing them in that spot only, repairing the roadbed, and then re-laying the blocks.
- This means that even without specialized knowledge or experience, continuous dissemination and maintenance can be managed by local workers.
- The IBP Project team hopes many interested participants will join this activity.
- If interested, please get in touch with Mr. Ismael Alulu (ialulu@mid.gov.sb) at MID Yard.
Steps of the Interlocking Block Production Process:
- Step 1: Grease the inside of the plastic molds.
- Step 2. Measure the weight of the cement.
- Step 3: Measure the sand, aggregate, and water using the pre-marked 10-liter bucket.
- Step 4: Place the aggregate into the mixer and add 14 ounces of water, then start the mixer.
- Step 5. Add cement, sand, and the remaining water to the mixer and mix until the ingredients are mixed.
- Step 6. Pour out the mixed concrete and scoop it into the plastic molds.
- Step 7. Put the filled molds on the vibrating table and vibrate them until evenly spread and smoothed.
- Step 8. Allow the filled molds to remain in place overnight for curing.
- Step 9. Remove the plastic molds the following morning.
- Step 10. Transport the cured blocks to the storage yard.

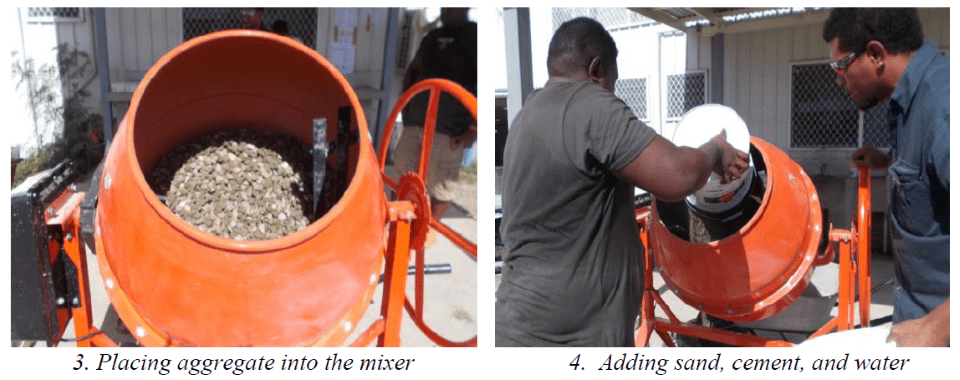
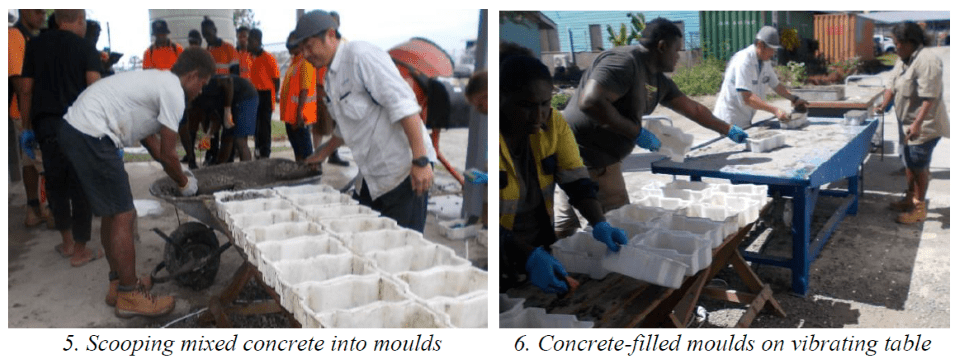
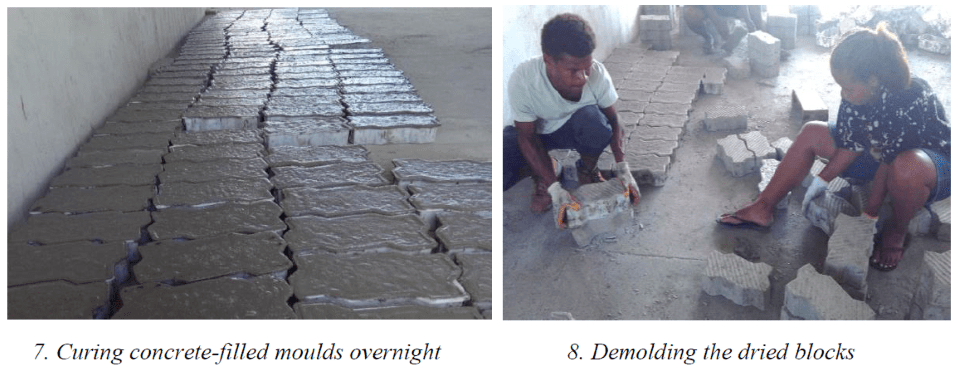
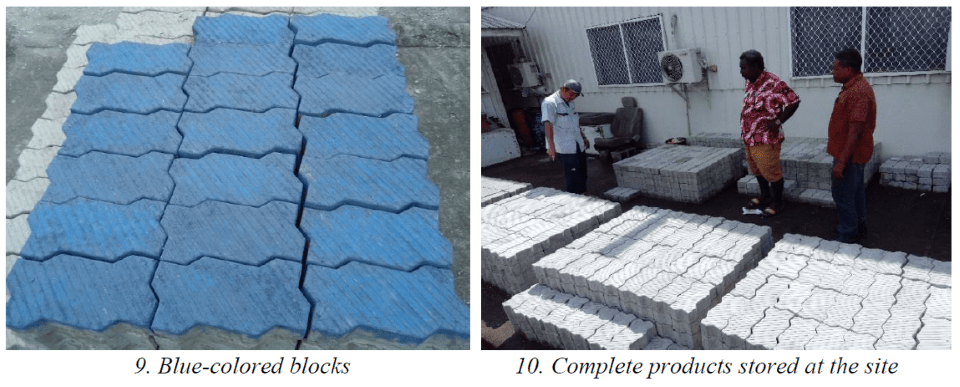
Source: JICA & MID Joint Release